“A key element in the automation of material flow is RFID, which is used for inbound and outbound logistics.
When a truck pulls in to deliver goods for the factory, the RFID system registers items in the delivery directly to the company’s SAP offering instant availability information.”
Benefits
+ 60 %
Productivity
20+
Robot
Error free
Loading process
Seamless
Material Flow
Starting Point
In 2011 the Breakers and Switches factory in Vaasa, Finland, manufactured roughly 80 % of all ABB products in that category. The ABB Group management set a key initiative to increase the productivity of the factory.
The means: AUTOMATION. A three-year investment plan was made and set to action.
The Turck Vilant Systems Solution
A key element in the automation of material flow is RFID, which is used for inbound and outbound logistics. When a truck pulls in to deliver goods for the factory, the RFID readers register each item in the delivery directly to the company’s SAP offering instant availability information.
As ABB is ready to deliver a Customer Order, each handling unit is will be monitored with the help of RFID. The company SAP system will finalize paperwork, after which all the handling units are moved to outbound freight area and loaded onto delivery trucks. The loading process is monitored and verified with the help of RFID ensuring an error free loading process.
Today the factory is nearly fully automated with 20+ robots, automated forklift trucks and seamless material flows. As a result, the productivity of the factory has increased 60% and volumes are growing.
ABB is a globally leading power electronics and automation company with presence in more than 100 countries. The business divisions are electrification products, robotics, industrial automation and power grids. ABB strives to be a leader in digitalization of industrial equipment and systems and serves 70 million connected devices.
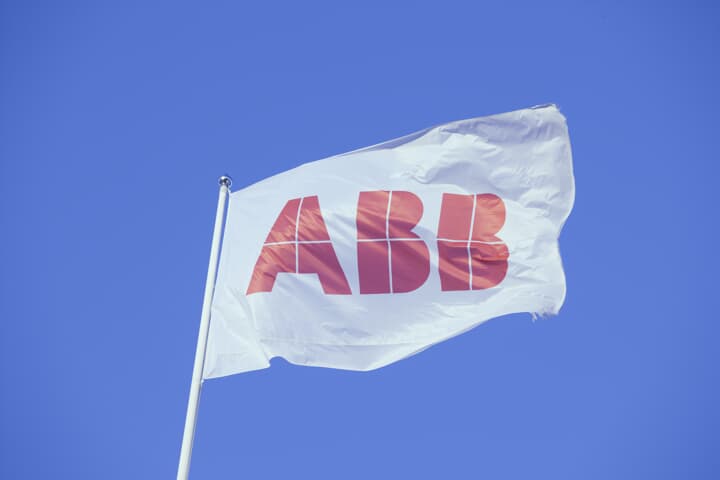